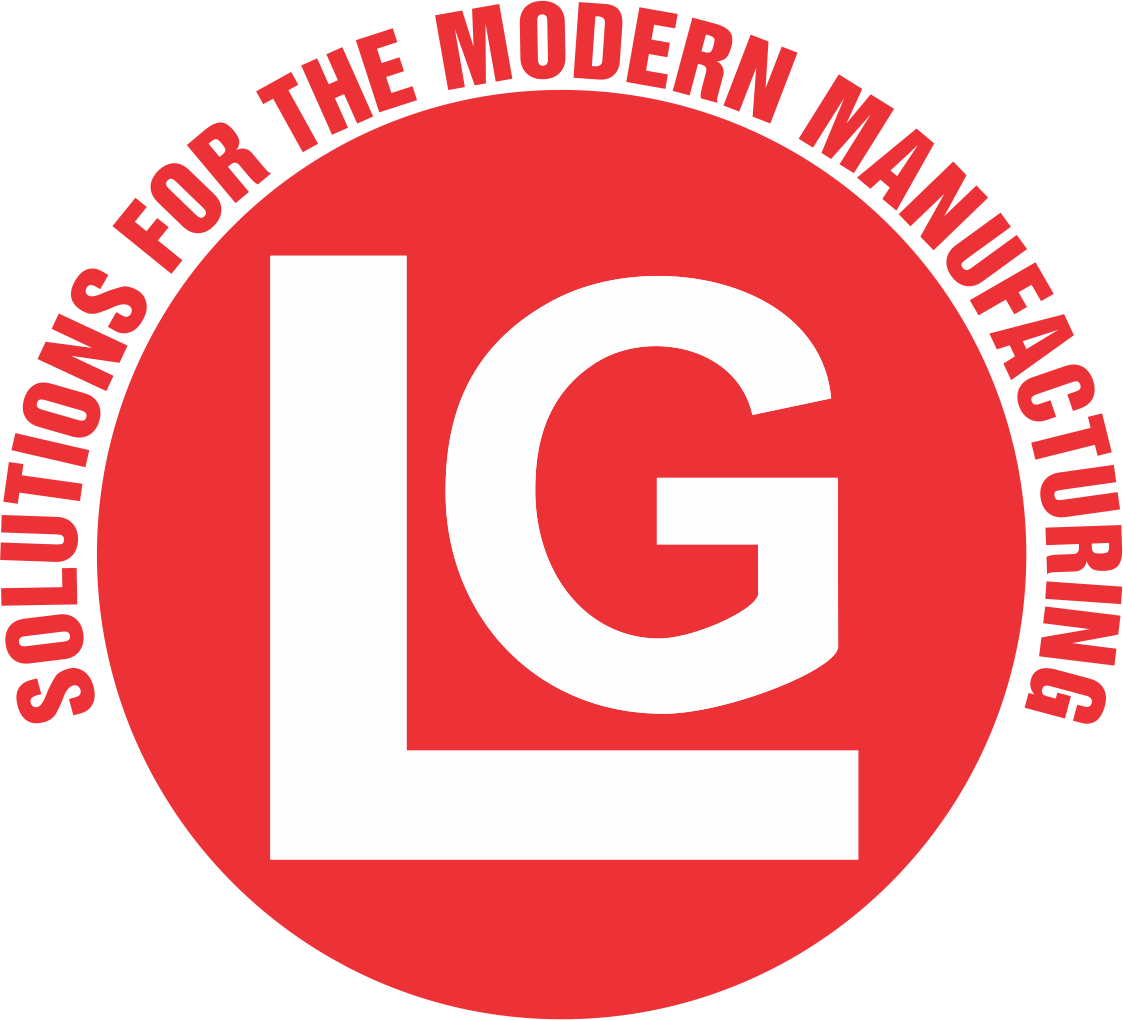
Dust collection and air filtration system for the mineral industry
The mineral industry works with various types of ores and rocks – from asphalt to cement, gypsum to lime. Each of these materials presents unique environmental challenges when it comes to filtration technology for dust collection systems:
BWF Envirotec provides filtration technology for dust collection systems in the air filtration industry, focusing on productivity. Ensuring product quality and compliance with dust emission limits are key objectives of our industrial filters. Specific requirements for industrial filters in dust collection systems include features such as high abrasion resistance, electrostatic dissipation, and strong chemical resistance.
Industrial dust collection systems for the mining sector require specialized industrial filters.
BWF Envirotec filters provide complex technical solutions for all filtration processes. We offer a wide range of industrial filters and services to manage dust in various production processes.
We assist our customers in achieving their production goals. To accomplish this, we analyse dust sample and industrial filter for all filtration applications in our laboratory, propose system optimization & solutions, and provide training on filtration media, industrial filters, and operational know-how at our Training Academy
PM-Tec ® và Needlona ® -
Dust filtration solutions in the cement industry.
The flexibility of our filters for the mining industry is demonstrated as follows:
A few references parameters regarding filtration systems in the mining industry.
Dust sources |
System filter material |
Location |
Amount |
Input load g/Nm 3 |
Operating temperature / Max °C |
Cement - clinker cooler |
Needlona ® NO/NO 551 CS52 |
Iran |
1.000 |
20 |
160/200 |
Cement - Chlorine bypass |
Needlona ® PTFE/PTFE 704 MPS CS30 |
Germany |
1.200 |
35 |
170-175/190 |
Lime, gypsum and clay Industry - Shalf kiln |
Needlona ® PTFE/PTFE 704 MPS CS30 |
France |
572 |
10 |
170-175/190 |
Lime, gypsum and clay Industry - Rotary kiln |
PM-Tec ® GL 750 |
South Africa |
6,532 |
20 |
110-160 |
Cement - Rotary kiln |
PM-Tec ® GL 750 |
Brazil |
7.800 |
80 |
150/210 |
Asphalt industry |
Needlona ® NO/NO 401 CS17 AsphalTec |
France |
480 |
250 |
80/130 |
Advantages of our filters for your industrial dust collection system:
PM-Tec ® và Needlona ® -
Persuasive filtration solutions for all industrial filtration systems.
The PM-Tec® and Needlona® filter bags are custom-designed to meet the requirements of the dust removal process in the dust collection system. This provides customer with the optimal technical solution for their filtration system. We offer filter bags for all types of dust collection systems and applications, along with corresponding support cages.
Depending on the method of cleaning the filter tubes, the high-efficiency filter media of the bags is enhanced with various surfaces, functions, or protective finishes. These features provide better protection for the filter environment against harmful mechanical and chemical influences. As a result, separation efficiency is improved, effective cleaning is ensured, dust emissions are minimized, and the lifespan of the filter bags in the dust collection system are extended.
Needlona® Filter Bags for Industrial Filtration Systems
- Filter material made from all common polymer fibers.
- The fiber coating of the filter bags is applied to a robust support fabric, making the filter material extremely compact, dimensionally stable, and mechanically resistant for long service life in the harshest conditions.
PM-Tec® Filter Bags for Industrial Filtration Systems
- Filter material made from needlefelt or fiberglass fabric.
- Equipped with a multi-layer, high-efficiency ePTFE membrane.
- Fine dust particles are separated on the surface of the filter bag.
Filter bags suitable for all applications in dust collection systems
Silo systems, packing stations, and conveyor belts
Filters for silos, packing stations, and conveyor systems are loaded with dry dust, mainly in ambient conditions. Therefore, economically efficient Needlona® needle felt made from polyester can be used. The additional Cementsurf ® finish helps reduce friction between dust and fibers, which not only enhances the cleaning efficiency but also extends the lifespan of the filter bags in the dust collection system.
Cement mill, separators
The high dust load in the dust collection system from cement plants or separators requires a durable filtration media. In countries with relatively high humidity, the CS17® oil- and water-repellent finish should be used to ensure that accumulated dust is not only separated but also efficiently cleaned from the filter bags. The addition of grinding aids imposes high demands on the filtration environment, as these aids prevent cement dust from clumping, thereby increasing the efficiency of the mill. Limited buildup behavior significantly hinders dust separation, making MPS® or PM-Tec® filter bags the most effective choice for use in dust collection systems.
Coal grinding and drying
Because the drying process accompanies the milling, the moisture in the air is always high, which leads to chemical attacks on polyester fibers due to hydrolysis, weakening their strength over time. Therefore, BWF Envirotec combines chemically sensitive but mechanically stable polyester fibers with chemically stable but mechanically weaker polyacrylonitrile fibers to create filter bags that optimize both lifespan and profitability in this complex environment. Due to the risk of dust explosions, we recommend using the ExCharge ® antistatic filtration media to safely discharge static electricity.
Clinker cooler
Hot clinker dust emitted from cement kilns is usually cooled by ambient air before further processing. Since this dust is handled in a dry state and does not contain harmful gases, using filter bag material made from m-aramid can provide a long service life and economic efficiency. m-Aramid is characterized by its higher stable temperature resistance with low air moisture, as well as reduced mechanical abrasion due to the impact of abrasive clinker dust.
Bypass
The increasing use of secondary fuels today come with raising chlorine concentrations in exhaust gases and products to unacceptable levels. By extracting part of the flow from the cyclone preheater and then further cooling it, harmful gases can be effectively separated in solid form using filter bags. However, the consistently high temperatures and the corrosive composition of dust and gases require extremely durable filter materials which PTFE are the perfect solution for effective filtration material in these dust collection systems.
Cement Kiln
A common method in cement kilns involves the use of a rotary kiln combined with a countercurrent cyclone preheater. In this system, intensive heat and material exchange occurs between the descending raw powder and the increase of exhaust gases. This process not only heats the raw powder but also promotes the binding of acidic components present in the exhaust gases, which can otherwise cause chemical damage to the filters positioned downstream.
This absorption process has become increasingly important with the growing use of secondary fuels. Long service life can be achieved with economical PPS filter bags when the inlet temperature of the filter remains below 150°C. Filter bags made from homopolymer polyacrylonitrile (DT) are also suitable if, thanks to intensive heat recovery, the filter inlet temperature is consistently reduced below 120°C and peak temperatures above 140°C are avoided. This results in further cost reductions. For higher temperatures, BWF Envirotec recommends using high-temperature-resistant fibers like polyimide fabric and fiberglass.